Lean fundamentals for employees
In terms of cost reduction and improving efficiency, lean is the most widespread methodology in the world. By learning and using the basics of lean, employees can significantly reduce unnecessary costs, improve productivity, optimize inventory, increase customer satisfaction, and respond more flexibly to market demands.
For whom do we recommend our Lean fundamentals for employees program?
Results of Lean fundamentals for employees program
Employees adopt a lean mindset and acquire the lean toolkit necessary for performing their tasks more efficiently. Participants understand the benefits of lean, learn about its tools, and know how to apply them. They identify inefficient processes and waste factors in their own areas of work and can propose improvements. With more efficient work practices, they feel less overwhelmed and have more time to recharge. Their managers will be more satisfied with their performance and trust them more. Employees will have a greater influence on the company’s success and operations, and their opinions will be valued, enhancing their satisfaction and commitment. They become self-directed and self-managing, creating more comfortable workflows and a clearer, more pleasant work environment.
Themes and process of the programme
Participants in the program will understand the concept, philosophy, and process of lean.
Simulation exercise for either services or production.
Participants become acquainted with the 7+2 types of waste.
Waste hunting: participants identify the recognized wastes in practice within their own work areas.
Mastering lean toolkits to effectively reduce losses and waste.
Attendance
In-Person
Recommended group size
14-16 participants
Duration
2 days
Available in
Hungarian
VSM (Value Stream Mapping) consultancy, lean culture diagnosis
On request
Format
Training
Recommended for
Employees
Have any further questions regarding our Lean fundamentals for employees program?
Please provide us with your contact details and our training expert will reach out to you shortly. Or feel free to contact them via one of the options below!
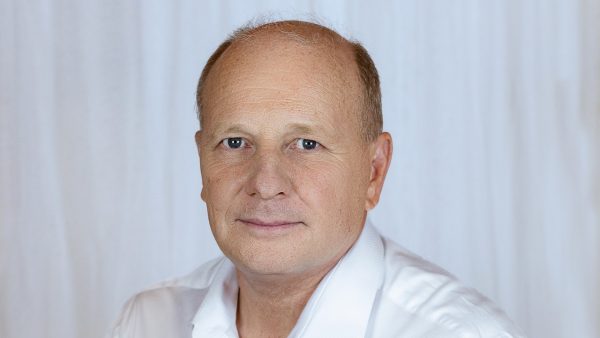
Zoltán Merkert
Lean business unit manager, senior trainer-consultant