Lean fundamentals for leaders
Mastering the basics of Lean, thus Lean fundamentals training for leaders is crucially important in the production and service sectors. This process-oriented management method, originating from Japan, minimizes expenditure waste and resource cost, improves efficiency, and helps create real quality value.
For whom do we recommend our Lean fundamentals for leaders program?
Lean methodology, originating from Japan’s automotive industry, is a process-oriented management approach that minimizes waste and improves the efficiency of production, service, and administrative processes. It addresses how to create the highest quality value for the customer using the least resources, time, and energy. Managers must learn Lean to effectively manage it later. It focuses on creating the highest quality value for customers with the least use of resources, time, and energy. Managers need to learn lean to effectively implement it. This training is ideal for leaders looking to make their organisations and teams more flexible, reduce costs, and boost productivity. It is designed for managers who want their employees to work independently at a high level, improve internal processes, gain a market advantage, and see immediate, visible returns. It provides a competitive edge over rivals.
Results of Lean fundamentals for leaders program
Themes and process of the programme
Basics of lean philosophy.
7+2 types of waste.
Method for identifying and reducing waste.
New methods, tools, and principles for process management and improvement.
Mastering lean toolkits.
Leadership skill development, that is essential for sustaining the lean methodology continuously within the organisation.
Practical applicability of lean.
Simulation exercises related to services or production.
Competencies of successful leadership include situational leadership, communication, motivation, and time management.
Attendance
In-Person
Recommended group size
8-12 participants
Duration
4 days
Available in
Hungarian
Format
Training
Recommended for
Top executives and middle managers
VSM consulting, lean culture diagnosis, 360 degree leadership diagnosis
On request
Have any further questions regarding our Lean fundamentals for leaders program?
Please provide us with your contact details and our training expert will reach out to you shortly. Or feel free to contact them via one of the options below!
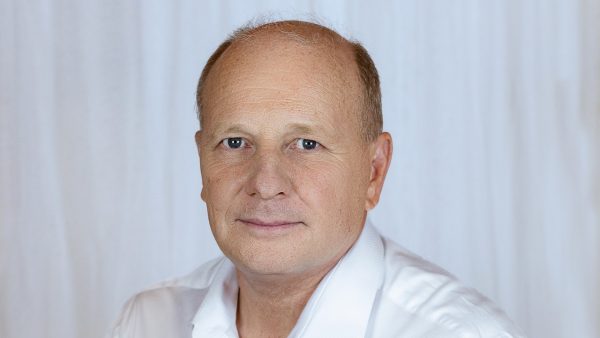
Zoltán Merkert
Lean business unit manager, senior trainer-consultant